Hydraulic cylinders, as the terminal actuators of hydraulic systems, play a vital role in ensuring stable and efficient system performance. Their quality directly determines whether the hydraulic system can operate smoothly, with sufficient force and precision. If the cylinder fails, the entire system may suffer downtime or reduced effectiveness. Therefore, understanding how to assess the quality of hydraulic cylinders is essential for both manufacturers and end users.
Hydraulic Cylinder Buffer: Absorbing Shock and Reducing Wear
A buffer mechanism is typically installed at the end of the hydraulic cylinder’s stroke. Its main function is to gradually reduce the speed of the piston as it approaches the end cover, thereby minimizing the impact caused by inertia and internal pressure. Without a buffer, the collision between the piston and end cap could cause mechanical damage, noise, and shortened cylinder life.
What Makes an Effective Buffer?
- The buffer should absorb significant kinetic energy in a limited stroke to avoid damage.
- The pressure within the buffer chamber must increase smoothly to avoid pressure spikes. Ideally, peak pressure should not exceed 1.5 times the rated cylinder pressure.
- As the kinetic energy converts into heat, the oil temperature must stay within safe limits to avoid degrading seals and hydraulic fluid.
There are different types of buffer designs, such as fixed or adjustable throttling, and the choice depends on the application. In heavy-duty machines like presses or excavators, an effective buffer system can extend the cylinder’s life and reduce maintenance frequency.
Internal and External Leakage: A Major Sign of Cylinder Quality
Internal leakage occurs when oil flows from the high-pressure chamber to the low-pressure chamber. This issue often results in reduced force output, lower efficiency, and erratic motion. According to the industry standard JB/T53378-1994, acceptable internal leakage rates are clearly defined based on pressure class and cylinder type.
External leakage, on the other hand, refers to oil seeping out from the piston rod, end seals, or port connections. Not only does this waste hydraulic oil, but it can also contaminate the environment, damage other machine components, and signal deeper mechanical problems.
To minimize leakage, manufacturers use precision-machined parts, quality sealing materials (such as PTFE or polyurethane), and multi-stage sealing systems. Proper installation and correct alignment are also essential.
Additional Factors for Judging Cylinder Quality
Apart from buffering and sealing performance, high-quality cylinders also demonstrate:
- Smooth surface finishes on the inner bore and piston rod to reduce friction and wear
- High concentricity and coaxiality to avoid uneven loading
- Hard chrome plating or other anti-corrosion treatments for outdoor or harsh environments
- Strict manufacturing tolerances, verified by pressure and leakage tests before delivery
Choosing the Right Cylinder for Your Application
When selecting a hydraulic cylinder, don’t just focus on price. Consider:
- The operating pressure and stroke length required
- Whether the environment includes dust, moisture, high temperature, or corrosive elements
- The mounting method (flange, clevis, trunnion, etc.)
- The need for customization or standardized replacements
Consulting with experienced manufacturers can help you select a cylinder that fits your specific system needs.
Maintenance Matters: Extend the Life of Your Hydraulic Cylinders
Even the best cylinder won’t last without proper care. Daily and periodic maintenance should include:
- Visual inspection of seals, rods, and connections for wear or leakage
- Monitoring oil cleanliness — dirty oil accelerates wear
- Lubricating moving parts when required
- Checking alignment to avoid side loading
- Keeping the system within temperature and pressure limits
Preventive maintenance not only avoids downtime but also ensures the entire hydraulic system remains reliable and efficient.
Conclusion
To sum up, judging the quality of hydraulic cylinders requires a comprehensive look at their buffering performance, sealing integrity, mechanical structure, and overall design. In addition to choosing a suitable cylinder based on actual needs, routine maintenance plays a decisive role in maximizing performance and extending service life.
By selecting the right product and maintaining it properly, you’ll enhance the durability and stability of your hydraulic system—and avoid costly repairs in the long run.
When working with special types like HC thin hydraulic cylinders, proper valve selection becomes even more critial. Details here.
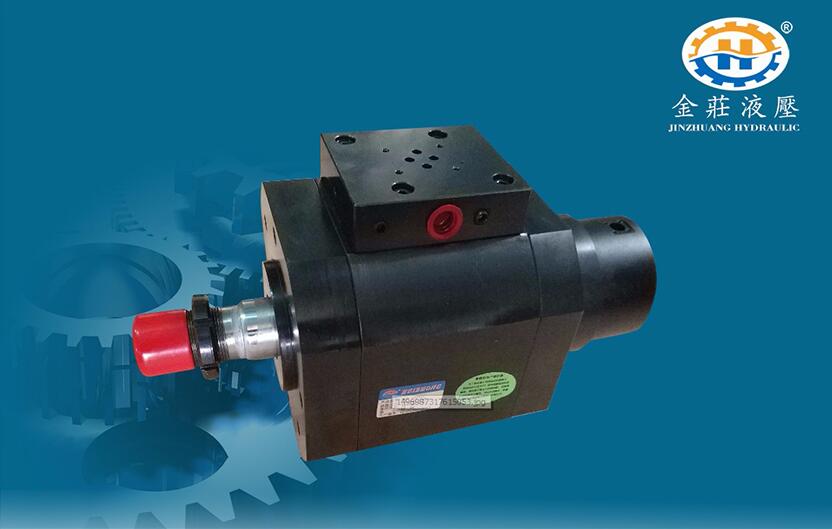